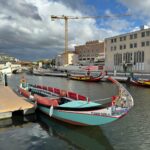
Moliceiros in Aveiro will be electric by the end of 2025
The transition from the current moliceiros (typical Portuguese boats) to the electric version covers the 27 boats currently operating in the Ria de Aveiro and
3D printing reduces construction time, energy consumption, carbon emissions and material waste. Get to know this Litehaus project.
Litehaus, an innovative real estate development company, is going ahead with the construction of the first 3D printed houses in Portugal, incorporating technology and sustainability.
It is a complex of 13 houses built in Portela da Villa, in Torres Vedras, based on technologies such as Artificial Intelligence (AI), at an early stage of creativity and design, and 3D printing, when in the construction phase. “We are here to distrust the industry. This technology allows us to produce up to 45 m2 of walls in just 20 hours,” said Simi Launay, Litehaus’ Chief Creative Officer (CCO), in a statement.
Speaking to Peggada, Launay explained that the production of a house using 3D printing and modular technology “consumes less energy mainly through the efficiency of materials and optimized production”, since “only what is needed is printed and there is no excess material”.
The modules are built with Eco-mortar, a material produced with a smaller carbon footprint than traditional cement (40 to 50% less CO2 emissions), and only the necessary items are transported, “eliminating the need to transport other machines and unused items”.
By investing in the production of modular buildings and 3D-printed houses, which consume 67% less energy to manufacture, the company is bringing a sustainable and innovative solution to the housing construction industry, which is responsible for 42% of carbon emissions.
With energy efficiency also in mind, the Litehaus team works on developing energy-efficient units with lower running costs for buyers. “Our goal is to achieve energy class A in order to optimize energy consumption. Our modules can be adapted to the specific needs of the environment. In addition, we make sure that the design is more efficient and saves costs on services such as heating or cooling, through double walls with insulation,” Launay told Peggada.
Litehaus’ goal is to build 100 houses a year in Portugal. Over the next two years, the company hopes to hire ten more people, as a way of growing and promoting local employment, according to the CCO.
“Litehaus is embarking on a mission to redefine living spaces, fusing AI technology, 3D printing and modular homes to create buildings that echo simplicity, innovation and sustainability. Our goal is to build 70% faster and 20% cheaper, building homes that epitomize elegance and minimalism harmonized with Portugal’s natural beauty,” adds Simi Launay. By reducing construction time, Litehaus is able to avoid consumption related to the logistics of supplying materials, but also to the movement of workers.
The transition from the current moliceiros (typical Portuguese boats) to the electric version covers the 27 boats currently operating in the Ria de Aveiro and
Quinta da Quinhas has opened in Vila Praia de Âncora to provide shelter for those passing through on their way to Santiago de Compostela, but
A new study by Deloitte concludes that ‘green’ skills and jobs are no longer limited to the traditional ‘green’ areas of the economy and that
This article promotes an action that encourages the reduction of waste generation through prevention, reduction, recycling, and reuse.
➡️ To discover more businesses that are aligned with Sustainable Development Goal 12 “Sustainable Production and Consumption” click here.
➡️ For news, tips and interviews about this topic, click here.
➡️ Want to know more about the 17 United Nations Sustainable Development Goals? Click here
Esta publicação também está disponível em:
Português (Portuguese (Portugal))
Para estar a par de tudo o que acontece na área da sustentabilidade, consumo responsável e impacto social.